MÉTODO 8D PARA LA SOLUCIÓN Y ANÁLISIS DE PROBLEMAS
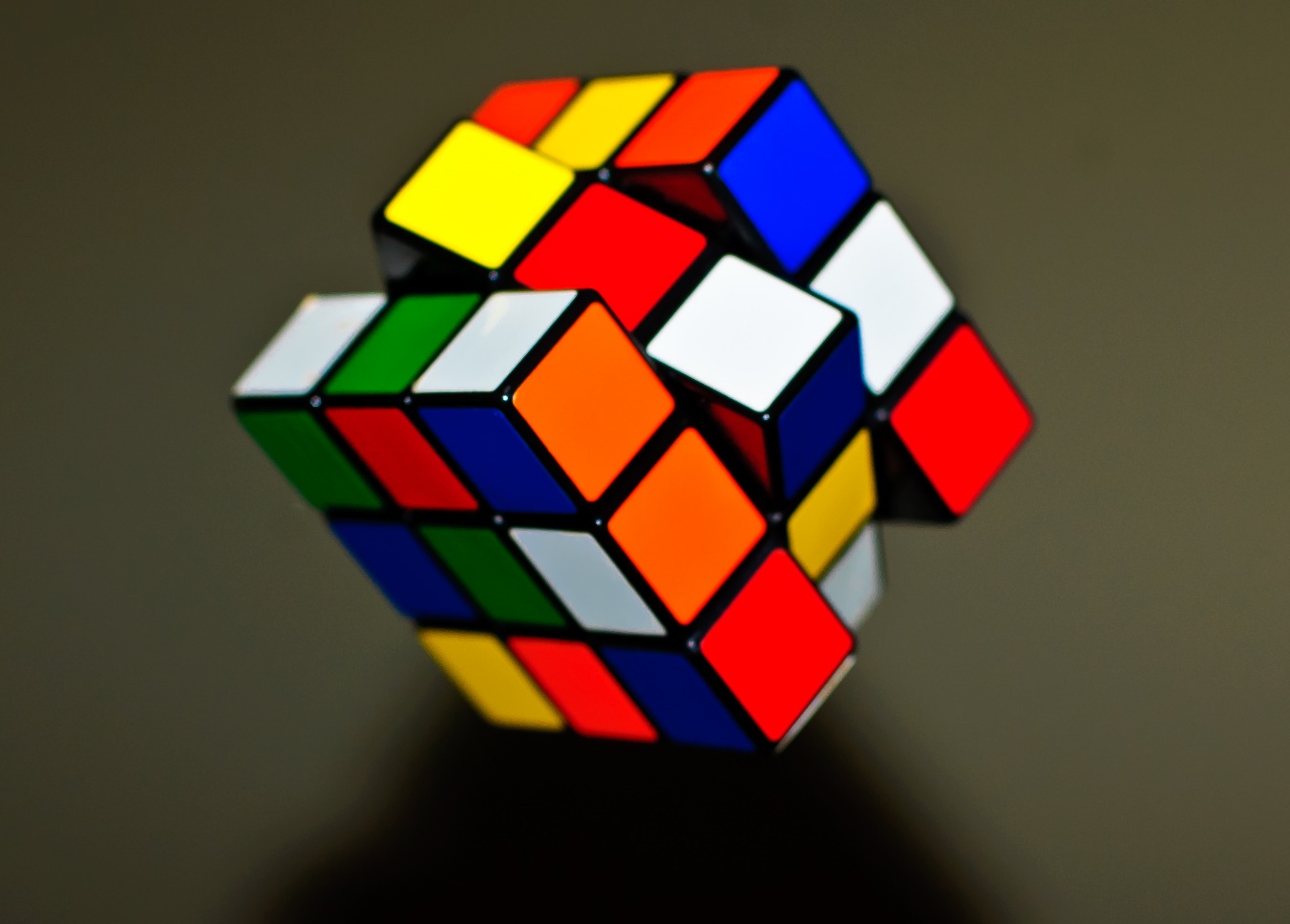
Dentro de las empresas o negocios cada día se presentan retos o problemas que hay que atender, definiendo la mejor estrategia para lograr los mejores resultados. Dependiendo de la densidad del problema podemos implementar una u otra solución. En algunos casos basta con nuestra experiencia o intuición para salir a flote, pero en ocasiones no significa que hayamos solucionado de raíz el problema, ya que en algunos casos se puede confundir una disminución de los síntomas con una solución definitiva, siendo esto el principal causante para que un mismo problema se presente una y otra vez dentro de las organizaciones. Pero antes de profundizar más, definamos lo que es un problema.
¿QUÉ ES UN PROBLEMA?
Si acudimos al diccionario de la Real Academia Española de la Lengua nos ofrece las siguientes acepciones:
1. m. Cuestión que se trata de aclarar.
2. m. Proposición o dificultad de solución dudosa.
3. m. Conjunto de hechos o circunstancias que dificultan la consecución de algún fin.
4. m. Disgusto, preocupación. U. m. en pl. Mi hijo solo da problemas.
5. m. Planteamiento de una situación cuya respuesta desconocida debe obtenerse a través de métodos científicos.
Todas estas definiciones suenan interesantes, pero vamos a concentrarnos en la 3 y 5. Vamos a plantear un problema como todo aquello que nos interpone un obstáculo para la productividad personal o empresarial, aquellas situaciones que perjudican nuestros intereses o los intereses de nuestro grupo. Es importante recalcar que todo problema tiene una solución, si no existe una solución, entonces no es un problema.
MÉTODO 8D
Enfocándonos en las alternativas que existen para la solución de problemas, vamos a concentrarnos en el método denominado “Ocho disciplinas para la resolución de problemas” o método 8D, este fue un método implantado durante la segunda guerra mundial, producto de las inconformidades en el proceso para la producción de armamento. Fue en los años 60 y 70 cuando la compañía Ford adoptó este método, convirtiéndose a la postre en el método estándar para la industria automotriz. La misma compañía Ford creo el estándar global 8D en los años 90, que es una readaptación del 8D.
El método 8D está enfocado a problemas industriales complejos, pero aun así es posible aplicarlo a problemas mas sencillos, simplificando el método y extrayendo los elementos básicos. A continuación, te presento una visión general del método.
Los puntos 1,2,3 se refieren a la detección de los problemas, el punto 4 se refiere al análisis de las causas y finalmente los puntos 5,6,7 y 8 a la implementación de las soluciones.
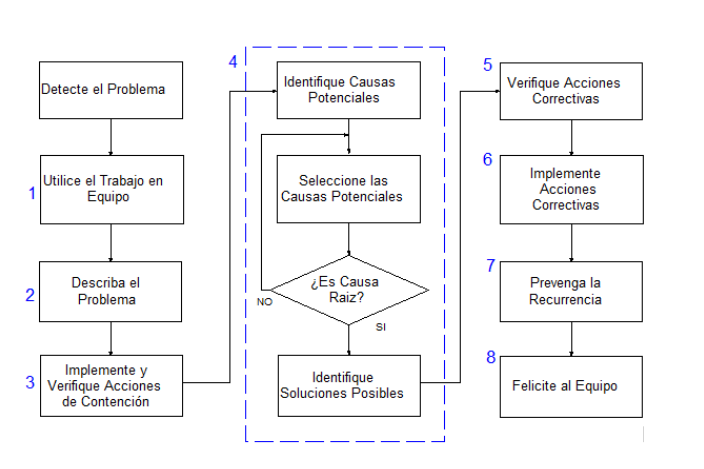
1. DETECTE EL PROBLEMA
Como una etapa previa será necesario documentar todos los síntomas que se están detectando. Es importante apoyarse en indicadores de satisfacción del cliente para este punto, además de indicadores internos sobre el clima organizacional. A lo largo del método 8D será importante el trabajo en grupo, y en esta etapa previa no será la excepción, así que será importante organizarse con el fin de realizar una tormentas de ideas que permita una detección mas completa de los problemas, una vez realizada esta detección se podrán tomar medidas una contención urgente
2. UTILICE EL TRABAJO EN EQUIPO
Como ya se mencionó en el primer punto, será muy importante el trabajo en equipo. Así que en este punto será necesario organizar a un grupo de personas expertas para que realicen un análisis a los problemas detectados. Como en todo grupo de trabajo existirá una persona responsable, además será necesario proveer de recursos, tiempos y procedimientos a este grupo de trabajo, dar las herramientas para que se puedan ofrecer los resultados en el menor tiempo posible.
3. DESCRIBA EL PROBLEMA
“Un problema bien definido es un problema medio resuelto”
En está etapa el equipo de trabajo deberá traducir todos los problemas en una definición detallada y clara, que permita una comprensión profunda para una posterior solución. Esta descripción deberá ser cuantificada, se deberá tener un contacto directo con los interesados y con las personas involucradas en los procesos, esto ayudará a obtener información relevante que podrá ser añadida a la descripción del problema.
4. IMPLEMENTE Y VERIFIQUE ACCIONES DE CONTENCIÓN
En la etapa previa a la detección, mencionamos la aplicación de medidas urgentes. Pero ahora en este punto nos enfocaremos en medidas que ataquen en una primera instancia los efectos que se detectaron en las etapas previas, estas medidas aun serán provisionales, ya que aun no se llegan a medidas correctivas definitivas. Será importante tener bien identificadas estás medidas de contención, ya que serán eliminadas una vez que se determinen las definitivas.
En esta etapa, el objetivo principal es poder aislar las causas de problemas, identificarlas claramente para establecer medidas correctivas posteriormente. Para hacerlo de una manera eficaz se sugiere lo siguiente realizar un listado con las causas potenciales, y posteriormente seleccionar de esta lista un conjunto principal. A esta lista podríamos llamarlo las causas de primer nivel o causas raíz.
5. VERIFICAR ACCIONES CORRECTIVAS
Cuando se tengan identificadas estas causas, entonces se podrán establecer medidas correctivas. Pero ¿Cómo sabremos que estas medidas son las correctas?, pues bien, necesitaremos tomar en cuenta los siguientes puntos:
Tendremos que realizar una evaluación previa para analizar que resultados son los que esperamos con estas medidas, estableciendo restricciones de tiempo, restricciones económicas y de alcance.
Identificar los riesgos que se puedan presentar al implementar estas medidas, tratando de evitar un impacto negativo colateral.
Definir los indicadores necesarios que nos permitan determinar si los efectos son los adecuados o los esperados.
Especificar medidas adicionales para detectar un posible fallo en su etapa inicial, para evitar que este fallo se arrastre hasta etapas maduras de nuestros procesos.
Te recomendados revisar nuestros articulo de los 5 Porqués y del diagrama Causa Efecto o Espina de Pescado, te servirán bastante en este punto.
6. IMPLEMENTAR ACCIONES CORRECTIVAS
En este punto se tendrá que detallar un plan de acción con los siguientes elementos:
Definir claramente los objetivos de cada acción correctiva.
Establecer los recursos de personas y tiempos necesarios para alcanzar a cumplir con estos objetivos.
Definir los costos monetarios de implementación para estas acciones.
Calendarizar los plazos de tiempo
Definir el o los responsables de cada acción.
7. PREVENGA LA RECURRENCIA
Es importante asegurarse que un problema no se vuelva a repetir, por lo tanto, se recomienda Analizar extenuantemente todos los procedimientos en donde se originaron los problemas con el fin de mejorarlos. La evolución de estos procesos deberá de estar en una evolución constante adaptándose al entorno competitivo y buscando la mejora continua de calidad.
8. FELICITE AL GRUPO
Como paso final dentro de este método, una vez aplicadas las acciones se deberán auditar los resultados para validar la eficacia del sistema, volver a revisar el proceso para analizar errores y buenas prácticas. Al final esto nos ayudará a obtener un listado de lecciones positivas que se deberán de conservar. Es muy importante al final de todo, reconocer el esfuerzo del equipo por su gran contribución a la mejora de la organización.